What To Consider
Before getting started, you will need to take stock of what your community needs, what assets you have to produce, and what capabilities your staff and volunteers have. It is also important to consider what rules you must follow when making PPE and other medical supplies.
Deciding What to Make
Deciding what to make may be informed by your understanding of local needs, but also from your available tools, supplies, and human resources. The Open Source Medical Supplies project library is a resource that can help you find designs and lists over 195 designs between 44 categories of PPE and medical supplies. Categories range from bias tape makers and mask pleaters to more complex items such as thermometers, nasopharyngeal swabs, and noninvasive ventilation helmets. As you browse the Project Library, you can filter on the designs by tools needed, medical status, and difficulty by clicking on the “Attributes” tool on the left side of the page.
OSMS has tracked over 47 million items produced by OSMS members and affiliates across the globe since March 2020. These production numbers and more data are available on our Impact Data section. The following medical supplies are popular projects within the OSMS Community:
You can read more about Personal Protective Equipment and its use to protect against different levels of risk in the OSMS PPE Use Guide.
Design Development

doctor-maker collaboration, and their husband-wife partnership!
If you are answering the call to innovate and develop a medical supply design, makers have been most successful when partnering with professionals in an institution that needs what they’re designing. This creates a dynamic where the need is based on real demand, the requirements are grounded in real-world application, and the institution that would use the design is already invested in the outcome. There are many inspired examples of these collaborations in the OSMS Project Library, including the Reeser Intubation Box. Cosmic Medical’s open source projects, including a bubble helmet and a snorkel mask are also a wonderful example of collaboration across different industries.
If you have a design in progress, we recommend sharing your open source project with the Open Source COVID19 Medical Supplies Facebook group first for feedback. This group has over 70,000 members and offers tremendous insight from a wide range of experts and brilliant amateurs. They can help you work through any design challenges or other problems with your project that you are facing.
Submitting a Design to the OSMS Project Library
Once your design is finalized, you may submit to the OSMS Medical Research Team via the OSMS Project Library design submission form. OSMS accepts submissions for both new, original designs as well as improvements made on existing projects. There are some considerations you should take before submitting your design, including gathering documentation for your project, field testing it, and sourcing the community for feedback before submission. Once your design has been submitted, the OSMS medical team will reach out to you if they have any further questions.
Project License Types
Open Source Medical Supplies utilizes Creative Commons licensing (specifically Attribution-ShareAlike 4.0) for its own website and content. We have found that Creative Commons allows us to quickly, easily and formally determine how information and data gets shared to others in ways we are comfortable with. We suggest explicitly sharing your design using one of the many variations of Creative Commons licensing for simplicity.
Medical Device Rules and Regulation
Medical devices are highly regulated items, and that regulation will vary depending on which state or country the supplies are being made and used in. These regulations are for a good reason — depending on the type of device, lives are on the line, and standards have been devised over time to ensure quality that keeps people safe.
In the United States, for example, medical supplies are categorized into three levels that range from low-risk devices like bandages, to medium-risk like surgical gloves and syringes, to high-risk items that are very important to sustaining lives, such as ventilators. All three classes of medical supplies and devices are regulated, evaluated, and approved by the Food and Drug Administration (FDA). The FDA doesn’t just approve a design; it also approves the manufacturing facility and process that creates the design. Getting FDA approval to produce medical supplies can take years.
Emergency Use Authorizations
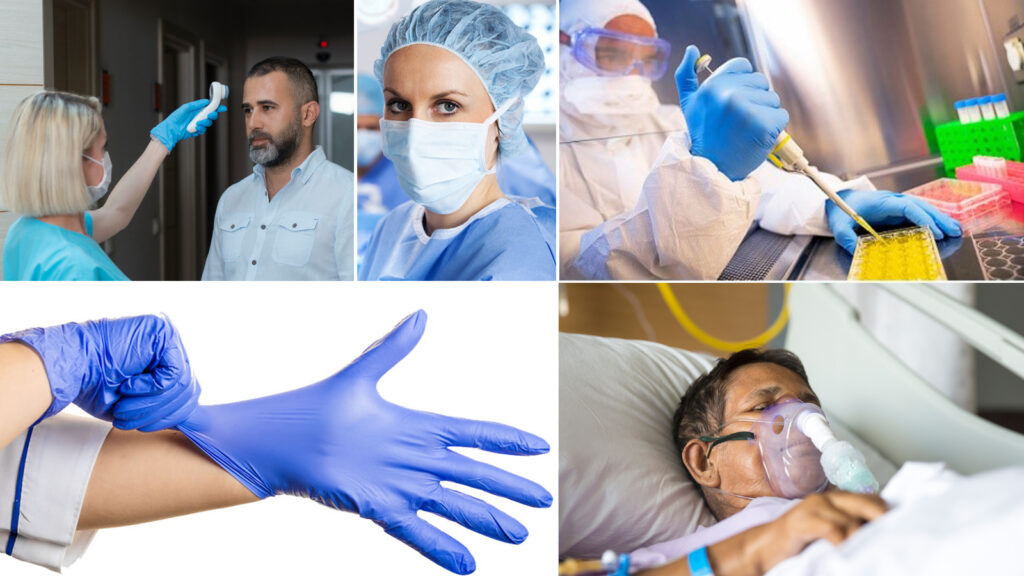
showing some items covered under its issuance.
When the COVID-19 pandemic began in the United States, and China shut down its factories during its 780 million person quarantine, the United State’s Food and Drug Administration (FDA) issued a Coronavirus Disease 2019 (COVID-19) Emergency Use Authorizations for Medical Devices (EUA). Emergency Use Authorizations have allowed device manufacturers much more flexibility in creating low-risk products such as face shields and cloth masks, and device-specific authorizations have allowed the FDA to move much faster when evaluating potentially life-saving new products that need to be approved for worst-case scenario use. Functionally this “EUA” is the window within which locally-made, non-FDA approved medical supplies are operating within.
Despite the EUA, it is recommended to attempt to the best of your ability and circumstances to follow regulations, which may seem cumbersome, but exist for good reason. Regulatory standards that apply to the supplies and devices in question, along with some helpful links are listed below:
Authorizations Outside of the U.S.
In England and Wales, the Social Action, Responsibility and Heroism (SARAH) Act seeks to provide protection to individuals who act voluntarily to provide reasonable aid to those who are injured, ill, in danger, or otherwise incapacitated. The Bill, passed by parliament in 2015, contains language to make clear its overarching purpose: “to take a range of measures to encourage volunteering and involvement in social action”.
The Access to Medical Treatments (Innovation) Act 2016, also applicable to England and Wales, was enacted “…to promote access to innovative medical treatments (including treatments consisting in the off-label use of medicines or the use of unlicensed medicines) by providing for (a) the establishment of a database of innovative medical treatments, and (b) access to information contained in the database.”
If you are familiar with similar laws in other countries, please reach out to us with relevant references.
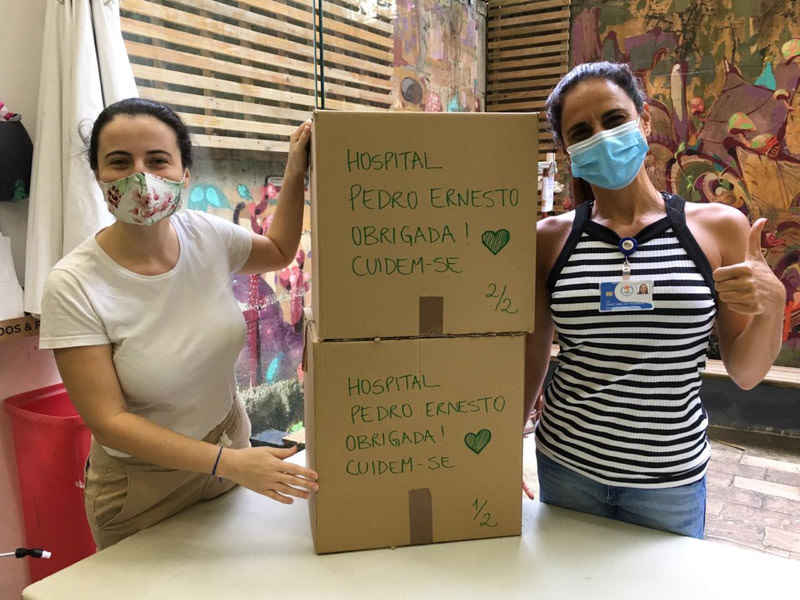
How to Get Approval
Each country has unique regulatory pathways. Helpful Engineering is a partner of OSMS and an international NGO that is, in part, dedicated to supporting engineers, designers and makers through approval processes. Join their Slack community and then look through the #qa-ra (Quality Assurance and Regulatory Affairs) channel. You can also reach out to them directly with a question.
Protecting Yourself and Organization from Liability
In the United States, Good Samaritan laws offer legal protection from civil lawsuits to people who voluntarily provide reasonable aid to those who are injured, ill, in danger, or otherwise incapacitated. A claim of negligent care can also be raised if the injuries or illness were made worse by the volunteer’s negligence. Laws generally do not exempt a Good Samaritan who acts in a willful, wanton or reckless manner in providing care, advice, or assistance.
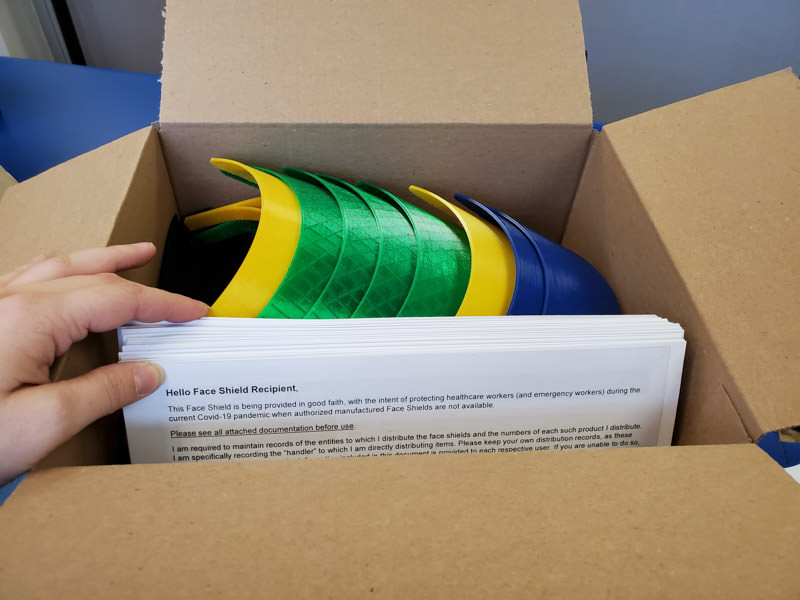
Good Samaritan laws only cover groups donating supplies. If you are selling PPE or supplies in the United States, you should investigate acquiring both general liability and product liability insurance for your business operations.
Universally, here are some additional best practices we’ve seen across the Local Response network:
Producing Supplies While Social Distancing
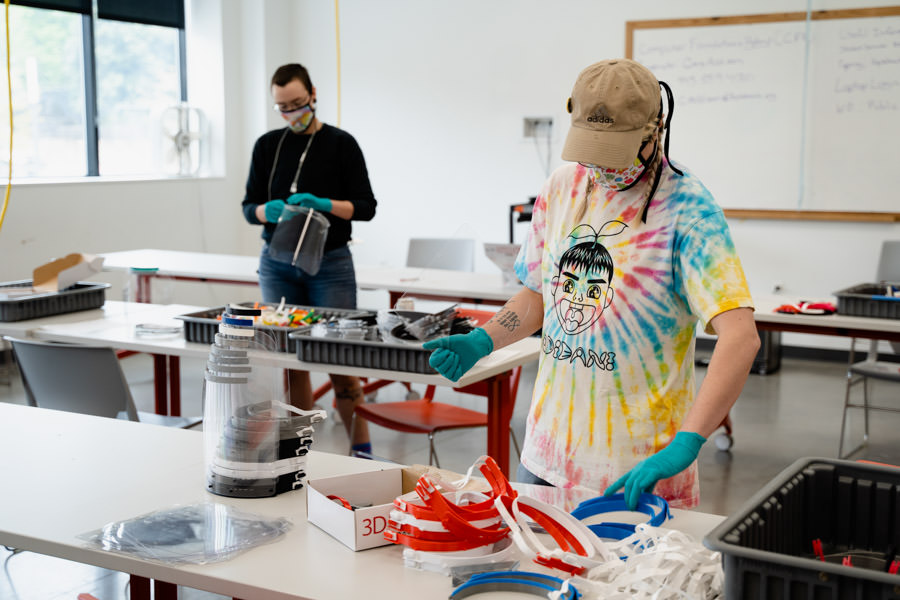
Production efforts have by and large been driven by the availability of materials, tools and medical supply requirements in local communities. Many groups use the Internet to communicate and have leveraged chat applications (Slack, Discord, Telegram, WhatsApp), social media (Facebook and Twitter), and cloud services (Google Suite and AirTable) to act as a distributed network, where people work individually and independently but pool their efforts for assembly or distribution. See the Community Organizing section of this guide for more on platforms and best practices.
Conversely, many types of medical supply production require a shared workspace. In these cases, teams have designed improvised workplaces and production lines that fulfill social distancing requirements.
Diving into your chosen design’s documentation will provide details and insight into best production practices. You are likely to discover whole forums associated with one design, with people happy to share expertise about workflows. The Open Source COVID-19 Medical Supplies Facebook group is also a good place to ask questions about best production practices, most effective designs, and more.